Common Questions Regarding Screw Air Compressor
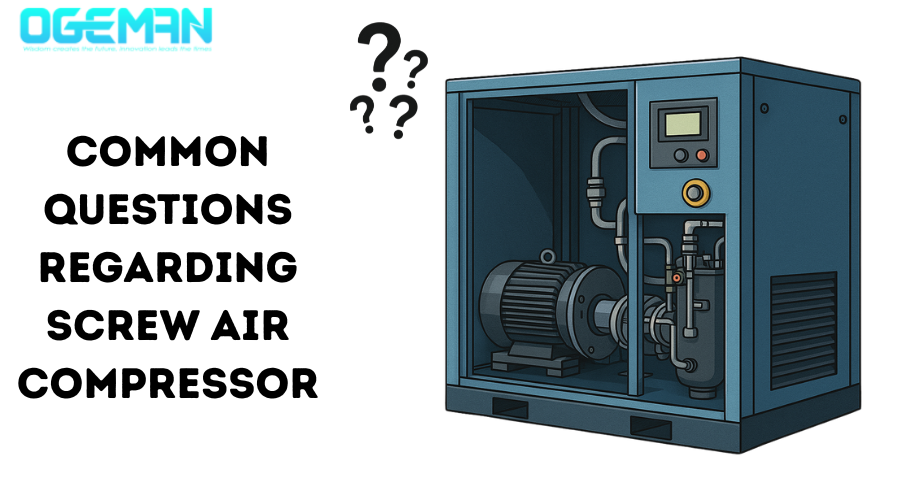
Construction, home repairs, automotive, and similar industries require machines to run pneumatic machines. Since too much air pressure is required, operators use air compressors to run those machines. It simplifies their tasks and increases the efficiency of overall operations. Screw air compressors are among the powerful machines that wind up lots of tasks by applying air pressure to pneumatic machines. In just a few seconds, an operator can perform strenuous functions with the help of these compressors. Since many people use them in the construction and automotive repair industries, they have questions about them. Let’s answer those queries to deal with all the challenges professionals and beginners face.
Are Screw Compressors Noisy?
No, they are much quieter than you expect. Some are quieter than even a usual vacuum cleaner. Therefore, you can consider them quiet in places like a garage, construction site, etc. Since there are different types available in the industry. A screw compressor is less noisy than a piston compressor. The reason behind its quiet operations is the use of rotary screws inside it. They generate low noise in the air compression process.
If you look at the noise level, screw compressors generate 65 to 75 dba noise. It is much lower than the piston type, which produces 80 dba and higher. However, you must inspect a few things to see if your air compressor makes noise. There could be problems with the mounting, crankcase, and parts inside it. Otherwise, a screw air compressor does not make much noise.
Is It OK To Leave the Air Compressor on All the Time?
It is made to work for long hours, even 24/7. You can keep it turned on all the time without any worries. However, every machine has a life and needs rest. A screw air compressor can work for many hours without breaks, but it is better to turn it off for some hours. Since it is a machine, it has an internal motor that can overheat. Once it exceeds its temperature limit, its components could wear and tear.
Giving it some rest when not using it will be a good choice. That will save its oil, filters, motor, and other components from early replacement. Unnecessary motor movement will affect the life of the screw air compressor, and it could reach its limit earlier than you imagine. Its motor will get excessive strain, and electricity will be wasted. Besides, compressor oil will soon be contaminated because of excess usage.
How much heat does a screw air compressor generate?
It does not generate too much heat if you look at its performance. Therefore, a screw air compressor can remain switched on for more than ten hours without any risk of overheating. If you compare it with other types, it generates less temperature than a piston air compressor.
A screw air compressor generates below 200 F heat, which is almost half of the heat generated by a piston compressor.
How Many Hours Is a Lot for An Air Compressor?
Every machine has an operating limit, which is also known as its life. When we talk about screw air compressors, it also has a limit. Since there are different types, each type has different lasting hours.
✅ Piston air compressors could last 50,000 hours.
✅ Oil-Free rotary screw compressors could last 70,000 hours.
✅ Rotary screw air compressors have 100,000 hours of life.
✅ Centrifugal air compressors have 250,000 hours of life.
What Is the Maximum Pressure for A Screw Compressor?
There are two stages in the screw air compressor; single-stage and two-stage compressors. A single-stage screw compressor can generate up to 250 PSIG (17 bar) pressure. At the same time, a two-stage screw compressor can generate up to 600 PSIG (41 bar) pressure.
What type of screw compressor is the most reliable?
An oil-lubricated screw air compressor is the most reliable one. It can last up to 10 years, which is a good enough time to have a return on investment. In other words, it can last up to 100,000 hours because of oil lubrication. Oil reduced the friction to keep the machinery going against all the challenges like heat and pressure. Even if used 24/7, it could last 6 years or 50,000 hours.
What Are Some Failures of Screw Compressors?
Every machine faces problems at least once in its life. Likewise, a screw air compressor also faces some challenges in the form of failures. These failures occur either because of lack of maintenance or overheating. Seals, gaskets, and other components must be replaced frequently if the machine usage rate is high.
✅ If it fails to reach maximum pressure, it is because the inlet or outlet pipe is blocked.
✅ Motor overloading failure is caused by clogged air filters or intake valve problems.
✅ Air filter problems could overheat the motor, so you must inspect it often.
✅ Excessive oil consumption occurs because of high oil levels, blocked return pipes, or faulty oil separators.
✅ Oil leakage occurs because of a damaged oil seal.
✅ Startup issues occur because of electrical problems like broken cords, fuse, coil, and switch problems.
✅ If there is low air pressure, it is because of air leakage.
✅ Excessive noise and vibration occur because of bearing issues or loose components.
✅ If moisture is in the air, you must inspect its air dryer.
Can A Screw Compressor Be Serviced?
Yes. A screw compressor can be serviced and periodic maintenance can help it to operate flawlessly and also maximize the service life. The structure of screw compressor consiss of several moving parts which usually become worn out with continuous usage.
Periodic Maintenance
✅ Periodic Oil and Filter Changes: The oil serves as a lubricant and coolant in an oil-injected screw compressor. Oil changes at the recommended intervals are made to reduce mechanical wear and help maintain efficiency. Cascaded air, oil, and separator filter scheduling will also have to be adhered to.
✅ For Cleaning and Checking Coolers: When dust and dirt accumulate, coolers gradually become less effective at cooling. Cleaning will help avert the overheating conditions.
✅ Checking and Replacing Belts and Couplings: Drive belts and couplings are the means of transmitting power to the compressor and they will wear out. Periodically checking the signs of wear and tear and replacing when needed will prevent untimely breakdowns.
✅ Draining Moisture from the System: Because moisture accumulates in the system of the compressor, it causes corrosion. Therefore, the drain moisture collects regularly to have clean dry compressed air.
✅ Checking for Leaks and Abnormal Noises: Also checking hoses and pipes, and joints, with regard to leakages, vibration, and sounds can warn early for failure detection.
Minor Repairs
✅ Air Leak Repairs: Compressed air leaks maximize inefficiency and raise energy payments. Locating and sealing the leaks will enhance performance.
✅ Replacing Worn-Out Bearings and Seals: Bearings and seals on shafts eventually wear; their replace- ment will avoid greater breakdowns.
Intensive Repairs
✅ Air-End Cleaning/Replacement: The air-end-comprised of rotors and housing-is the heart of a screw compressor. If the performance is not up to the mark then cleaning becomes necessary
✅ Motor Overhaul or Replacement: The electric motor driving the compressor can wear. Rewinding or replacing brings back the efficiency.
✅ Control Panel with Sensor Replacement: Contemporary compressors with electronic control might need recalibration or replacement after some time.
Conclusion
These were some of the common questions people ask online regarding screw air compressors. If you face these problems, this blog will certainly help you. They will also help users maintain their air compressors in good form.
Featured Articles
Construction, home repairs, automotive, and similar industries require machines to run pneumatic machines. Since too much air pressure is required, operators use air compressors to run those machines. It simplifies their tasks and increases the efficiency of overall operations. Screw air compressors are among the powerful machines that wind up lots of tasks by applying air pressure to pneumatic machines. In just a few seconds, an operator can perform strenuous functions with the help of these compressors. Since many people use them in the construction and automotive repair industries, they have questions about them. Let’s answer those queries to deal with all the challenges professionals and beginners face. Are Screw Compressors Noisy? No, they are much quieter than you expect. Some are quieter than even a usual vacuum cleaner. Therefore, you can consider them quiet in places like a garage, construction site, etc. Since there are different types available in the industry. A screw compressor is less noisy than a piston compressor. The reason behind its quiet operations is the use of rotary screws inside it. They generate low noise in the air compression process. If you look at the noise level, screw compressors generate 65 to 75 dba noise. It is much lower than the piston type, which produces 80 dba and higher. However, you must inspect a few things to see if your air compressor makes noise. There could be problems with the mounting, crankcase, and parts inside it. Otherwise, a screw air compressor does not make much noise. Is It OK To Leave the Air Compressor on All the Time? It is made to work for long hours, even 24/7. You can keep it turned on all the time without any worries. However, every machine has a life and needs rest. A screw air compressor can work for many hours without breaks, but it is better to turn it off for some hours. Since it is a machine, it has an internal motor that can overheat. Once it exceeds its temperature limit, its components could wear and tear. Giving it some rest when not using it will be a good choice. That will save its oil, filters, motor, and other components from early replacement. Unnecessary motor movement will affect the life of the screw air compressor, and it could reach its limit earlier than you imagine. Its motor will get excessive strain, and electricity will be wasted. Besides, compressor oil will soon be contaminated because of excess usage. How much heat does a screw air compressor generate? It does not generate too much heat if you look at its performance. Therefore, a screw air compressor can remain switched on for more than ten hours without any risk of overheating. If you compare it with other types, it generates less temperature than a piston air compressor. A screw air compressor generates below 200 F heat, which is almost half of the heat generated by a piston compressor. How Many Hours Is a Lot for An Air Compressor? Every machine has an operating limit, which is also known as its life. When we talk about screw air compressors, it also has a limit. Since there are different types, each type has different lasting hours. ✅ Piston air compressors could last 50,000 hours. ✅ Oil-Free rotary screw compressors could last 70,000 hours. ✅ Rotary screw air compressors have 100,000 hours of life. ✅ Centrifugal air compressors have 250,000 hours of life. What Is the Maximum Pressure for A Screw Compressor? There are two stages in the screw air compressor; single-stage and two-stage compressors. A single-stage screw compressor can generate up to 250 PSIG (17 bar) pressure. At the same time, a two-stage screw compressor can generate up to 600 PSIG (41 bar) pressure. What type of screw compressor is the most reliable? An oil-lubricated screw air compressor is the most reliable one. It can last up to 10 years, which is a good enough time to have a return on investment. In other words, it can last up to 100,000 hours because of oil lubrication. Oil reduced the friction to keep the machinery going against all the challenges like heat and pressure. Even if used 24/7, it could last 6 years or 50,000 hours. What Are Some Failures of Screw Compressors? Every machine faces problems at least once in its life. Likewise, a screw air compressor also faces some challenges in the form of failures. These failures occur either because of lack of maintenance or overheating. Seals, gaskets, and other components must be replaced frequently if the machine usage rate is high. ✅ If it fails to reach maximum pressure, it is because the inlet or outlet pipe is blocked. ✅ Motor overloading failure is caused by clogged air filters or intake valve problems. ✅ Air filter problems could overheat the motor, so you must inspect it often. ✅ Excessive oil consumption occurs because of high oil levels, blocked return pipes, or faulty oil separators. ✅ Oil leakage occurs because of a damaged oil seal. ✅ Startup issues occur because of electrical problems like broken cords, fuse, coil, and switch problems. ✅ If there is low air pressure, it is because of air leakage. ✅ Excessive noise and vibration occur because of bearing issues or loose components. ✅ If moisture is in the air, you must inspect its air dryer. Can A Screw Compressor Be Serviced? Yes. A screw compressor can be serviced and periodic maintenance can help it to operate flawlessly and also maximize the service life. The structure of screw compressor consiss of several moving parts which usually become worn out with continuous usage. Periodic Maintenance ✅ Periodic Oil and Filter Changes: The oil serves as a lubricant and coolant in an oil-injected screw compressor. Oil changes at the recommended intervals are made to reduce mechanical wear and help maintain efficiency. Cascaded air, oil, and separator filter scheduling will also have to be adhered to. ✅ For Cleaning and Checking Coolers: When dust and dirt accumulate, coolers gradually become less effective at cooling. Cleaning will help avert the overheating conditions. ✅ Checking and Replacing Belts and Couplings: Drive belts and couplings are the means of transmitting power to the compressor and they will wear out. Periodically checking the signs of wear and tear and replacing when needed will prevent untimely breakdowns. ✅ Draining Moisture from the System: Because moisture accumulates in the system of the compressor, it causes corrosion. Therefore, the drain moisture collects regularly to have clean dry compressed air. ✅ Checking for Leaks and Abnormal Noises: Also checking hoses and pipes, and joints, with regard to leakages, vibration, and sounds can warn early for failure detection. Minor Repairs ✅ Air Leak Repairs: Compressed air leaks maximize inefficiency and raise energy payments. Locating and sealing the leaks will enhance performance. ✅ Replacing Worn-Out Bearings and Seals: Bearings and seals on shafts eventually wear; their replace- ment will avoid greater breakdowns. Intensive Repairs ✅ Air-End Cleaning/Replacement: The air-end-comprised of rotors and housing-is the heart of a screw compressor. If the performance is not up to the mark then cleaning becomes necessary ✅ Motor Overhaul or Replacement: The electric motor driving the compressor can wear. Rewinding or replacing brings back the efficiency. ✅ Control Panel with Sensor Replacement: Contemporary compressors with electronic control might need recalibration or replacement after some time. Conclusion These were some of the common questions people ask online regarding screw air compressors. If you face these problems, this blog will certainly help you. They will also help users maintain their air compressors in good form.
READ FULLRotary screw compressors are widely used in various industries due to their efficiency, durability, and continuous operation capabilities. They are essential in manufacturing, construction, and industrial applications, where a constant supply of compressed air is required. Unlike piston compressors, rotary screw compressors offer smoother operation, lower maintenance costs, and higher efficiency. When selecting a rotary screw compressor, it is crucial to understand the three main designs available. Each design has unique features that make it suitable for specific applications. In this article, we will break down the three primary types of rotary screw compressors, their advantages, and how to choose the right one for your needs. 1. Oil-Injected Rotary Screw Compressors What Are Oil-Injected Rotary Screw Compressors? Oil-injected rotary screw compressors are the most common type used in industries requiring high power and continuous operation. These compressors use lubricating oil to cool and seal the compression chamber, ensuring smooth and efficient performance. How They Work ✅ Air Intake: The compressor draws in ambient air through an intake valve. ✅ Compression Process: The rotating screws trap and compress the air while oil is injected to reduce heat and friction. ✅ Separation Process: The compressed air and oil mixture pass through an oil separator, where the oil is removed and recycled. ✅ Final Delivery: The dry compressed air exits through the output port for use in industrial applications. Advantages ✅ Higher Efficiency: Oil lubrication reduces wear and tear, enhancing efficiency. ✅ Continuous Operation: Suitable for 24/7 industrial use. ✅ Longer Lifespan: With proper maintenance, these compressors last for years. ✅ Heat Dissipation: The oil cools the system, preventing overheating. Best Applications ✅ Manufacturing plants ✅ Automotive industry ✅ Food and beverage processing (with additional filtration) ✅ Textile industries 2. Oil-Free Rotary Screw Compressors What Are Oil-Free Rotary Screw Compressors? Oil-free rotary screw compressors do not use lubricating oil in the compression chamber. Instead, they rely on special coatings and advanced technology to minimize friction and heat buildup. How They Work ✅ Air Intake: The compressor pulls in ambient air. ✅ Compression Stage: Instead of oil, special materials like ceramic or Teflon coatings reduce friction. ✅ Cooling Process: These compressors often use air or water cooling systems to manage heat. ✅ Final Delivery: The compressed air is delivered completely oil-free. Advantages ✅ 100% Oil-Free Air: Ideal for industries requiring contaminant-free air. ✅ Lower Maintenance Costs: No oil changes are required. ✅ Eco-Friendly: Reduces the risk of environmental contamination. ✅ Compliance with Industry Standards: Meets strict ISO 8573-1 Class 0 air purity standards. Best Applications ✅ Pharmaceutical production ✅ Electronics manufacturing ✅ Food and beverage industries ✅ Hospitals and laboratories 3. Variable Speed Drive (VSD) Rotary Screw Compressors What Are VSD Rotary Screw Compressors? VSD (Variable Speed Drive) compressors are energy-efficient rotary screw compressors that adjust motor speed based on air demand. These compressors provide greater flexibility and energy savings compared to traditional models. How They Work ✅ Air Demand Monitoring: The compressor continuously monitors air demand. ✅ Speed Adjustment: The motor speed is adjusted accordingly, reducing energy consumption when demand is low. ✅ Compression Process: Similar to oil-injected or oil-free models, but with more precise control. ✅ Final Delivery: The compressed air is supplied with optimized energy use. Advantages ✅ Energy Savings: Reduces electricity costs by up to 50%. ✅ Extended Equipment Life: Less wear and tear due to variable speeds. ✅ Lower Carbon Footprint: Ideal for companies aiming to reduce emissions. ✅ Quiet Operation: Generates less noise compared to fixed-speed compressors. Best Applications ✅ Industrial automation ✅ Printing and packaging industries ✅ Automotive workshops ✅ Any facility with fluctuating air demand Choosing the Right Rotary Screw Compressor Selecting the best rotary screw compressor depends on your specific requirements. Here’s a quick guide: Feature Oil-Injected Oil-Free VSD Efficiency High Moderate Very High Air Purity Not 100% 100% Varies Maintenance Moderate Low Moderate Energy Savings Standard Standard Very High Best For Heavy-duty industries Sensitive applications Energy-conscious operations If cost and durability are your priorities, an oil-injected compressor is ideal. For clean and contaminant-free air, opt for an oil-free model. If energy efficiency and long-term savings matter most, a VSD rotary screw compressor is the best choice. Maintenance Tips for Rotary Screw Compressors Proper maintenance ensures optimal performance and longevity. Here are essential maintenance tips: ✅ Regular Oil Changes (for oil-injected models) ✅ Check and Replace Air Filters ✅ Inspect Hoses and Seals for Leaks ✅ Monitor Temperature Levels ✅ Drain Moisture from the System (especially in humid environments) ✅ Schedule Professional Inspections Annually Conclusion Rotary screw compressors are essential for industries requiring a continuous and reliable compressed air supply. Understanding the differences between oil-injected, oil-free, and VSD rotary screw compressors allows businesses to select the best model for their needs. While oil-injected compressors are the most durable, oil-free models ensure purity, and VSD compressors provide unmatched energy efficiency. By choosing the right type of rotary screw compressor, companies can optimize productivity, reduce costs, and improve operational efficiency. Investing in proper maintenance and high-quality equipment will ensure long-term performance and reliability. Do you have any questions about rotary screw compressors? Let us know in the comments!
READ FULLPrecision filters are devices designed to remove contaminants from fluids, including gases and liquids, with a high degree of accuracy. These filters are critical in applications where even the smallest impurities can cause significant issues, such as in pharmaceutical manufacturing, semiconductor production, and water treatment. The primary goal of a precision filter is to ensure that the fluid passing through it meets stringent purity standards, thereby protecting sensitive equipment and processes. Key Features of Precision Filters Understanding the key features of precision filters is essential for selecting the right filter for a specific application. Here are some of the most important features: High Filtration Efficiency Precision filters are known for their high filtration efficiency, which means they can remove a significant percentage of contaminants from the fluid. This efficiency is typically measured in terms of the filter's ability to capture particles of a specific size. Durability and Reliability Given their critical role, precision filters are built to be durable and reliable. They are often constructed from robust materials that can withstand harsh operating conditions and maintain their performance over time. Specificity One of the standout features of precision filters is their specificity. They can be designed to target particular types of contaminants, whether they are solid particles, microorganisms, or chemical compounds. Scalability Precision filters are available in various sizes and configurations, making them scalable for different applications. Whether you need a small filter for a laboratory setup or a large one for an industrial process, there's a precision filter to meet your needs. Low Pressure Drop A key performance metric for precision filters is the pressure drop across the filter. A low pressure drop means that the filter does not significantly impede the flow of fluid, which is crucial for maintaining system efficiency. Types of Precision Filters Precision filters come in several types, each suited to specific applications and types of contaminants. Here are some of the most common types: 1. Membrane Filters Membrane filters are widely used in applications requiring high levels of purity, such as in the pharmaceutical and food and beverage industries. These filters use a thin, semi-permeable membrane to separate contaminants from the fluid. 2. Depth Filters Depth filters capture contaminants throughout the entire thickness of the filter material, rather than just on the surface. This makes them ideal for applications where high contaminant loads are expected. 3. Cartridge Filters Cartridge filters are cylindrical filters that can be easily replaced when they become clogged. They are used in a variety of industries, including water treatment and chemical processing. 4. Bag Filters Bag filters use a bag-shaped filter element to capture contaminants. These filters are often used in applications where large volumes of fluid need to be filtered quickly. 5. HEPA Filters HEPA (High-Efficiency Particulate Air) filters are designed to remove at least 99.97% of airborne particles 0.3 microns or larger. They are commonly used in cleanrooms, healthcare facilities, and HVAC systems. 6. Activated Carbon Filters Activated carbon filters are used to remove organic compounds and chlorine from fluids. These filters are commonly used in water treatment and air purification systems. 7. UV Filters UV filters use ultraviolet light to kill or inactivate microorganisms in fluids. They are often used in water and air purification systems where microbial contamination is a concern. Applications of Precision Filters Precision filters find applications across a wide range of industries due to their ability to ensure fluid purity and protect sensitive processes. Here are some of the most notable applications: Pharmaceutical Manufacturing In pharmaceutical manufacturing, maintaining a contaminant-free environment is critical. Precision filters are used to purify water, air, and other fluids, ensuring that products meet strict quality standards. Semiconductor Production The semiconductor industry requires extremely pure water and chemicals for manufacturing processes. Precision filters are essential in removing even the tiniest particles and ions that could affect product quality. Water Treatment Water treatment systems rely on precision filters to remove impurities, such as bacteria, viruses, and chemical contaminants, ensuring that the water is safe for consumption and use. Food and Beverage Industry In the food and beverage industry, precision filters help maintain the quality and safety of products by removing contaminants from water, air, and other inputs. Healthcare and Laboratories Healthcare facilities and laboratories use precision filters to ensure a clean environment, protecting patients and ensuring accurate experimental results. Industrial Processes Many industrial processes, such as chemical production and oil refining, require precision filters to remove contaminants from raw materials and process fluids. HVAC Systems HVAC (Heating, Ventilation, and Air Conditioning) systems use precision filters to maintain air quality, removing dust, pollen, and other airborne contaminants. Choosing the Right Precision Filter Selecting the right precision filter for your application involves considering several factors: Contaminant Type Identify the type of contaminants you need to remove. Different filters are designed to target specific contaminants, so this is a crucial step. Filtration Efficiency Determine the level of filtration efficiency required for your application. This will help you choose a filter that can effectively remove the contaminants. Flow Rate Consider the flow rate of the fluid that needs to be filtered. Ensure that the filter you choose can handle the required flow rate without causing a significant pressure drop. Operating Conditions Take into account the operating conditions, such as temperature and pressure, that the filter will be exposed to. Choose a filter that can withstand these conditions. Maintenance and Replacement Consider the maintenance and replacement requirements of the filter. Some filters are easier to replace and maintain than others. Benefits of Using Precision Filters The use of precision filters offers numerous benefits: Improved Product Quality By removing contaminants, precision filters help ensure that the final product meets quality standards, whether it's a pharmaceutical drug, a semiconductor, or treated water. Equipment Protection Precision filters protect sensitive equipment from damage caused by contaminants, reducing maintenance costs and downtime. Regulatory Compliance Many industries are subject to strict regulations regarding fluid purity. Using precision filters helps companies comply with these regulations. Enhanced Efficiency By ensuring fluid purity, precision filters help maintain the efficiency of processes and systems, leading to cost savings and improved performance. Challenges in Precision Filtration While precision filters offer many benefits, there are also challenges to consider: Filter Clogging Over time, precision filters can become clogged with contaminants, reducing their efficiency. Regular maintenance and replacement are necessary to address this issue. Cost High-quality precision filters can be expensive, both in terms of initial investment and ongoing maintenance costs. Selection Complexity Choosing the right precision filter for a specific application can be complex, given the variety of options and factors to consider. Conclusion Precision filters are essential components in many industries, ensuring the purity of fluids and protecting sensitive processes and equipment. By understanding the features, types, and applications of precision filters, you can make informed decisions about their use in your specific context. Despite the challenges, the benefits of using precision filters far outweigh the drawbacks, making them a critical investment for quality and efficiency. As technology advances, we can expect to see even more innovative solutions in the field of precision filtration, further enhancing their effectiveness and sustainability.
READ FULL